An Innovative Approach to Blast Analytics Using Drone Technology for Enhanced Safety and Productivity
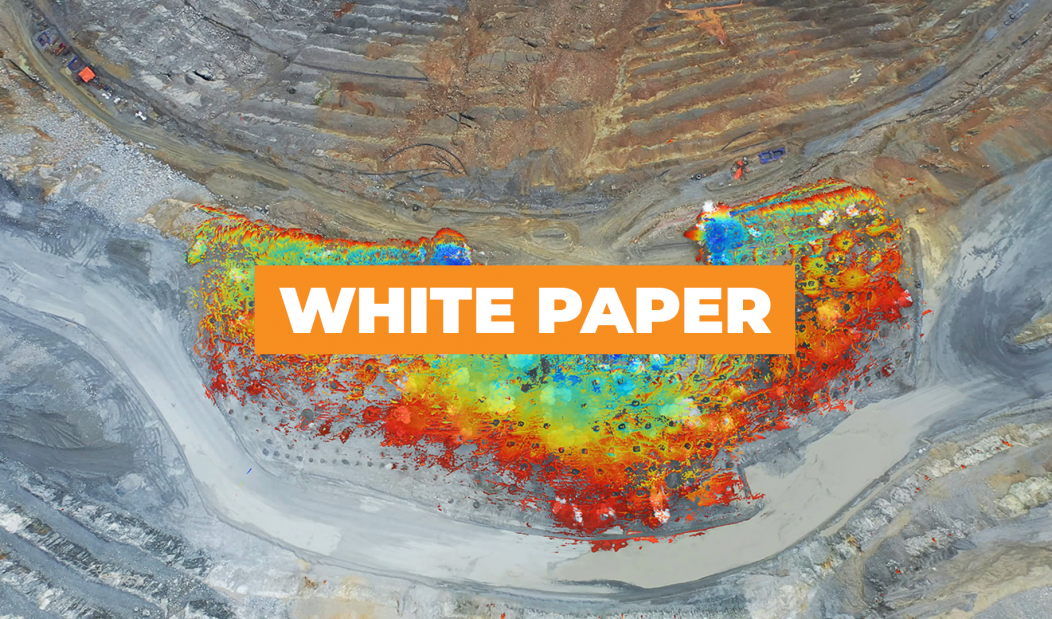
AUTHORS
Rahardian Dwitya, GroundProbe, Balikpapan, Indonesia
Taufan Nugraha, GroundProbe, Balikpapan, Indonesia
Dwi Prio Utomo, GroundProbe, Balikpapan, Indonesia
Ilham Prasetya Budhi, GroundProbe, Balikpapan, Indonesia
Rachmat Hamid Musa, GroundProbe, Balikpapan, Indonesia
Michael Jhonson Arnold Sirait, GroundProbe, Balikpapan, Indonesia
Nessy Salsabilita, GroundProbe, Balikpapan, Indonesia
Albert Giovanni Cabrejo-Lievano, GroundProbe, Tucson, USA
INTRODUCTION
The mining industry is transitioning towards technological optimisation and cost-effective operations, driven by automation, artificial intelligence, and machine learning advances. These technologies enable the industry to enhance efficiency, increase profitability, and improve safety. Consequently, mining companies increasingly invest in innovative technologies to optimise their operations and achieve cost savings, ultimately boosting profitability.
Conventional blasting practices often fail to increase productivity and reduce environmental risks. Poor blasting efficiency remains a significant impediment to mining efficiency. Enhancing blasting efficiency is crucial for all mining processes. However, recent technologies typically do not provide the comprehensive data necessary to improve efficiency and productivity and mitigate environmental hazards significantly. Current technological applications primarily focus on productivity aspects, such as rock fragmentation analysis, overlooking the broader impacts of blasting activities on safety.
Blasting activities can pose several hazards that impact productivity, including misfire holes, excessive blasting energy affecting slope stability, and flyrock. Between 1978 and 1993, four major causes of blasting-related injuries in surface mining operations were identified: lack of blast area security, flyrock, premature blasts, and misfires. During this period, 356 injuries were attributed to surface blasting operations, with flyrock accounting for 28.3% of the injuries, lack of blast area security for 41.2%, premature blasts for 15.7%, misfires for 7.8%, and other causes for 7% (Siskind and Kopp, 1995).
This paper introduces an innovative approach using advanced technology that can be adopted in blasting operations to achieve optimal productivity and safety. By leveraging new methods and tools, the mining industry can better address the challenges associated with blasting and enhance overall operational efficiency.
CHALLENGES
Blasting Impact on Wall Stabilisation
Large open-pit mines rely on economies of scale to meet their business targets (Stacey, 2009). Consequently, high-energy blasting and massive machinery capable of high productivity levels have become prevalent in these operations. However, the increasing energy concentration and production rates can compromise the integrity of pit walls. Therefore, disciplined and effectively controlled blasting strategies, which are not significantly compromised by short-term production demands, are essential to prevent wall damage. A successful wall control blasting strategy aims to produce a well-fragmented, loose muck pile while maintaining an on-design and undamaged slope, as illustrated in Figure 1.
![]() ![]() |
Figure 1. Damage control techniques are not applied (left), and damage control techniques are applied (right) (Karzulovic, 2007).
The geological characteristics of the wall surrounding the blast area and those further up the slope play a crucial role in determining the potential for blasting-induced damage. Effective blast designs for wall control must consider the properties of the rock mass. Major geological structures may pose risks to slope stability, as the high energy levels generated by blasts can cause structural failure or sudden rock mass movement. Thorough mapping of geotechnical hazards on the slope or wall is imperative, as these factors contribute to slope instability.
Safety Consideration of Flyrock
Flyrock is an undesirable outcome in any blasting operation, involving excessively thrown rock fragments that can exceed mine boundaries and cause damage to people, objects, and machinery. Even within designated danger zones, flyrock can result in human fatalities, injuries, and long-term damage to machinery and infrastructure (IME, 1997). Numerous studies have improved our understanding of flyrock causes, identifying key factors such as inappropriate delay time, improper blast hole patterns, insufficient burden, excessive charging, hole diameter, misfires, rock mass properties, and geological anomalies (Langefors and Kishlstrom, 1963; Holmeberg and Persson, 1976; Roth, 1979; Persson et al., 1994; Adhikari, 1999; Kecojevic and Radomsky, 2005; Mohamad et al., 2013; Mohamad et al., 2018).
Exceeding the safe radius of flyrock can harm equipment and humans. Safe zones typically range from 300 meters for equipment to 500 meters for humans, depending on rock characteristics, explosive strength, and surrounding tools or facilities. Reducing the exclusion zone could save operational costs, making it crucial to determine the maximum flyrock trajectory using empirical and dimensional analysis methods. Empirical methods are informed by Lundborg (1981) and Richard and Moore (2005), while dimensional analysis draws on Ebrahim Ghasemi’s theory (2012). An innovative approach for predicting flyrock distance is essential to potentially adjust exclusion zones, increasing productivity and safety.
Misfire and Out-of-Sequence Firing Occurrence
Blasting, a common technique for reducing the size of rock-bearing minerals, involves using explosives that require careful handling to avoid unexpected initiation. Understanding the causes of explosive misfires and controlling and preventing measures is crucial for improving industrial explosive usage. Misfires are a significant hazard in blasting operations, causing serious injuries and fatalities. Indications of misfires include inadequate ground movement, undisturbed ground, lack of fracturing, poor fragmentation, undetonated explosives, and hang-ups on the face (Taiwo et al., 2022).
After blasting, a thorough inspection of the face and muck pile is vital to prevent misfires and ensure safety. Hazards from undetonated explosives and the post-blast environment necessitate regular checks by trained personnel throughout the loading operation. All personnel must report any anomalies observed. Promptly determining the level and type of misfire is essential, and establishing a secure exclusion zone until explosive retrieval ensures safety.
SOLUTION
BlastVision®, a GroundProbe blast performance analytics tool, provides actionable insights from blast activity that can be used to make informed decisions. BlastVision® captures custom high-speed drone footage of blasts as they happen and converts it into analytical data for insights and decision-making.
Optimal results depend on drone position and camera gimbal angle relative to the blast pad. Configuring the camera gimbal at a 45° angle detects vertical blast hole movement (Figure 2). The drone should be positioned to fill the frame width, capturing stable points around the blast area. Detonations should occur towards the drone to prevent plume or rifling occlusion.
![]() ![]() |
Figure 2. Drone configuration is needed to capture the area of concern.
BlastVision® Workflow and Visualisation
Using advanced proprietary algorithms, BlastVision® converts the footage into analytics data using BlastVision® 2D and 3D software. The data is then remotely analysed and returned to the mine site personnel to optimise blasting, improve mine safety and productivity, and help control the impact of blasting on the surrounding environment.
The difference between 2D and 3D software lies in the output: BlastVision® 3D uses point clouds/3D surfaces for specific coordinate measurements. In contrast, BlastVision® 2D relies on raw footage analysis using visualisations like blend visualisation, luminance change detection, and contour analysis. The duration of the analysis depends on the findings and objectives.
![]() |
Figure 3. Workflow progress of BlastVision and Type of Visualisation.
BlastVision® generates visualisations that help on-site teams analyse blast performance and impact on adjacent areas. These are automatically produced from raw footage, analysing surface changes at each pixel (Figure 4). Visualisation sensitivity depends on video quality.
![]() ![]() |
Figure 4. BlastVision visualisation and pixel changes through the frame video.
BlastVision® 3D requires comprehensive point cloud data from pre-blast drone recordings of all interest areas. Aligning this data with blast design files provides actual blast hole coordinates (Figure 5).
![]() ![]() |
Figure 5. The point cloud area is aligned with the blast design.
RESULTS AND DISCUSSION
Wall Control Analysis
Using 30 blast recordings, luminance change detection and difference history visualisation identified fall-of-ground locations due to blast energy (Figure 6). Changes in pixel colour indicate fall of ground, with intensity reflecting the significance of the fall. Adjacent blast pads show more significant changes.
![]() ![]() |
Figure 6. Fall of ground detection by BlastVision Visualisation.
Zoom analysis features detect fall of ground, with colour intensity changes indicating the scale of the fall (Figure 7). Material detachment, rifling material, and sub-bench failure are detected.
![]() |
Figure 7. The zoom analysis feature is used to detect fall of ground.
Coordinates of fall-of-ground areas are plotted on the point cloud to provide detailed location information (Figure 8). Findings classify hazard areas into two domains at different levels, aiding geotechnical teams in risk assessment (Figure 9).
![]() |
Figure 8. Fall of ground coordinates plotting using point cloud of surface area.
![]() |
Figure 9. The potential hazard risk is based on the fall of ground observed during blasting as impacted by blast energy on the wall surface.
Flyrock Measurement
Analysing 20 blast videos, flyrock landing distances ranged from 30.4 to 370.5 meters (Table 1). BlastVision® software captures flyrock trajectories, measuring distance and initial velocity from source holes (Figure 10).
![]() |
Figure 10. Visualisation of flyrock trajectories.
Based on observations, the maximum flyrock distance was 370.5 meters, suggesting that the exclusion zone for machinery should be adjusted to 400 meters for increased safety and put some blasting control to prevent excessive flyrock (Figure 11).
Summary of Furthest Landed of Fly Rocks | Increase Exclusion Zone for Safety Consideration |
![]() |
![]() |
Figure 11. Increase the exclusion zone to increase the safety of equipment (unscaled image).
Evaluating excessive flyrock distances can inform blast design adjustments to control stemming configuration, explosive type, and charge weight, reducing flyrock and saving costs (Figure 12). Ensuring actual design implementation during blasts enhances safety and efficiency.
![]() ![]() ![]() |
Figure 12. Blast design evaluation is needed to reduce the excessive flyrock and optimise cost.
Blast Pattern and Misfire Detection
BlastVision® provides critical data for detecting misfires and out-of-sequence firing, essential for safety and optimal blast patterns. Integrating actual and design blast data in 3D reveals less movement in misfire holes, indicated by gaps in blend visualisation and anomalies in heaving estimations (Figure 13).
![]() |
Figure 13. Gaps in colour in blend visualisation and anomalies detected in the heaving estimator feature.
Zoom analysis and blast movement detectors confirm misfires, highlighting fewer movement areas (Figure 14). Identifying and addressing misfires promptly ensures operational safety and efficiency.
![]() |
Figure 14. Zoom analysis and blast movement detector capturing the misfire hole.
CONCLUSION
BlastVision® represents an innovative approach and technology developed to analyse the effects of blasting activities by converting drone footage into analytical data. This technology can be adopted in blasting operations to optimise productivity and address safety considerations.
The wall control analysis provided by BlastVision® offers valuable insights for on-site geotechnical teams. It enables the detection of potentially unstable walls by capturing fall-of-ground events with detailed coordinate information. This capability allows for more effective control of blasting energy and helps maintain wall stability.
The flyrock analysis focuses on safety by evaluating and potentially adjusting the exclusion zone for equipment, thus preventing incidents caused by flyrock. Additionally, it offers opportunities to reassess blast designs to reduce operational costs while maintaining safety and efficiency.
Furthermore, BlastVision® delivers critical blast analytical data that aids in detecting potential misfires and out-of-sequence movements. This functionality is essential for post-blast inspections, helping to prevent hazards associated with misfires and ensuring overall operational safety and efficiency.
REFERENCES
Adhikari, G. K. (1999). Studies on flyrock at limestone quarries. Rock Mechanics and Rock Engineering, 32(4), 291-301.
Balakrishnan, B., & Rai, P. (2021). An overview of flyrock and its prediction in surface mine blasting using soft computing techniques. Electronic Journal of Geotechnical Engineering, Indian Institute of Technology (BHU).
Eko, M. R., Haris, R. H., Lubis, J., & Deri, N. P. (2023). Study of flyrock to reduce safe radius from 500 m to 300 m on blasting quarry at PT Vale Indonesia, Sorowako, Luwu Timur, South Sulawesi. IOP Conference Series: Earth and Environmental Science.
Ghasemi, E. (2012). Development of an empirical model for predicting the effects of controllable blasting parameters on flyrock distance in surface mines. International Journal of Rock Mechanics and Mining Sciences, 2, 163-170.
Holmeberg, R., & Persson, G. (1976). The effect of stemming on the distance of throw of flyrock in connection with hole diameters. Swedish Detonic Research Foundation, Report DS, 1.
Institute of Makers of Explosives (IME). (1997). Glossary of commercial explosives industry terms. Safety publication, Institute of Makers of Explosives, Washington.
Karzulovic, A., & Sepúlveda. (2007). Open pit problems in engineering practice. In Y. Potvin (Ed.), Slope Stability 2007. Proceedings of 2007 International Symposium on Rock Slope Stability in Open Pit Mining and Civil Engineering (pp. 201-211). Australian Centre for Geomechanics, Perth.
Kecojevic, V., & Radomsky, M. (2005). Flyrock phenomena and area security in blasting-related accidents. Safety Science, 43(9), 739–750.
Lundborg, N., Persson, P. A., Ladegaard-Pedersen, A., and Holmberg, R. (1975). Keeping the lid on flyrock in open-pit blasting. Engineering and Mining Journal, vol. 176. pp. 95-100.
Lundborg, N. (1981). Risk for flyrock when blasting. Swedish Council for Building Research, BFR Report R29, Stockholm.
Langefors, U., & Kishlstrom, B. (1963). The modern technique of rock blasting. John Wiley and Sons, New York, USA.
Mohamad, E. T., Armaghani, D. J., Hajihassani, M., Faizi, K., & Marto, A. (2013). A simulation approach to predict blasting-induced flyrock and size of thrown rocks. Electronic Journal of Geotechnical Engineering, 18, 365-374.
Mohamad, E. T., Yi, C. S., Murlidhar, B. R., & Saad, R. (2018). Effect of Geological Structure on Flyrock Prediction in Construction Blasting. Geotechnical and Geological Engineering, 36(4), 2217–2235.
Persson PA, Holmberg R, Lee, J. (1994). Rock blasting and explosives engineering. Boca Raton, FL: CRC Press LLC.
Read, J., & Stacey, P. (2009). Guidelines for open pit slope design. CSIRO Publishing, Collingwood.
Richards, A., & Moore, A. J. (2005). Flyrock control-by chance or design. In Proceedings of 30th ISEE Conference on Explosives and Blasting Technique (pp. 6-8). New Orleans.
Roth, J. (1979). A model for the determination of flyrock range as a function of shot conditions. Management Science Associates, Altos, USA.
Siskind, D. E., & Kopp, J. W. (1995). Blasting accidents in mines: A 16-year summary. In Proceedings of the 21st Annual Conference on Explosives and Blasting Technique (pp. 224-239). Cleveland, OH: International Society of Explosives Engineers.
Taiwo, B. O., Abdulkadir, S. B., Moshen, J., Akisonde, K. A., & Oluwansanmi, E. A. (2022). Blasting misfire: A review of causes, economic effect, control and handling techniques. International Journal of Energy Research.
Verakis, H. C., & Lobb, T. E. (2003). An analysis of blasting accidents in mining operations. In Proceedings of the 29th Annual Conference on Explosives and Blasting Technique (pp. 119-129). Cleveland, USA.
– END –